Pneumatic Valves Essential Role in Modern Industry Explained
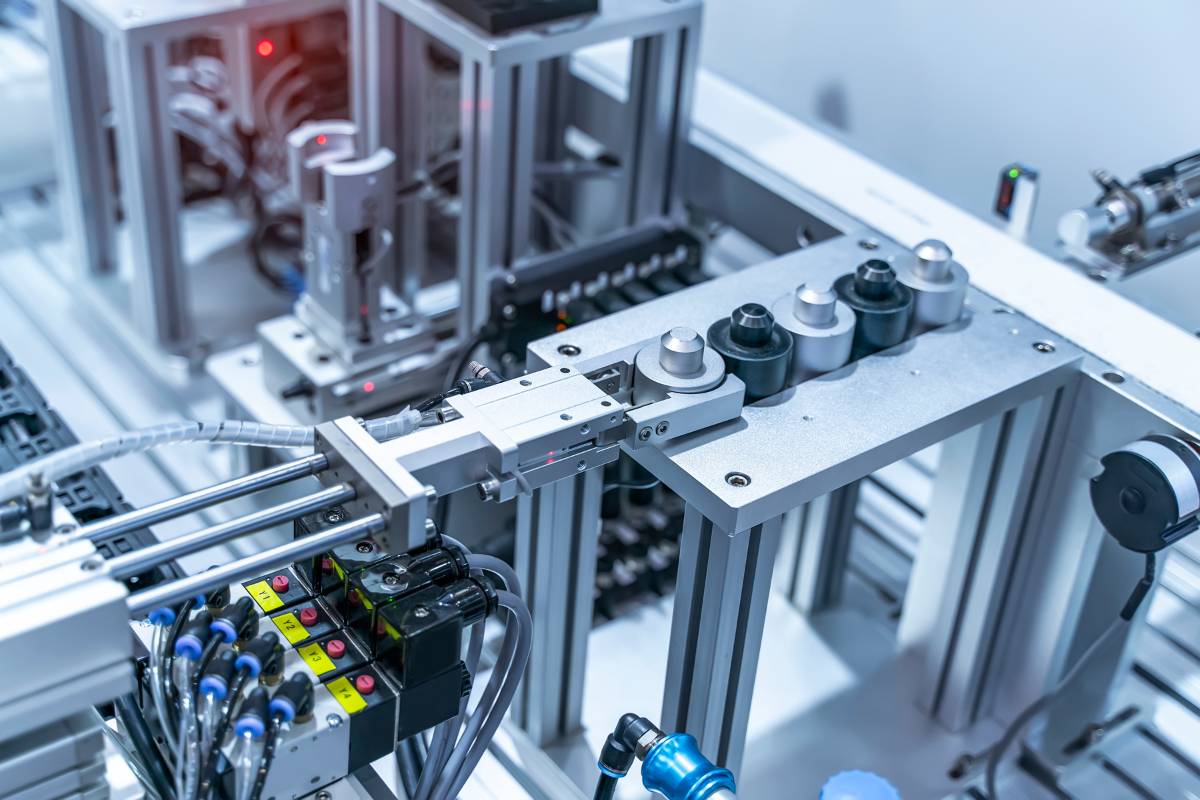
Pneumatic valves are crucial components of fluid power systems because they can accurately control and manipulate compressed air to power a range of industrial tasks. These devices are crucial control elements that allow automated motion, force, and speed regulation by regulating the direction, flow rate, and pressure of compressed air to actuators, cylinders, and other pneumatic components. Their employment in various industries, such as manufacturing, robotics, packaging, transportation, and medical technology, underscores their significance in modern automation.
Table of Contents
TogglePneumatic Valves – Understanding The Fundamentals
A thorough understanding of the fundamentals underlying pneumatic valve operation is essential for engineers, technicians, and operators alike. Making educated decisions throughout system design, component selection, installation, and maintenance requires using this knowledge base. Professionals can maximize system performance, improve efficiency, effectively troubleshoot faults, and guarantee pneumatic systems’ long-term dependability and safety by understanding the nuances of valve functioning. This knowledge is very helpful when working with sophisticated applications or specialty valves, like those designed by market leaders like Bürkert Fluid Control Systems.
Bürkert, recognized for its commitment to innovation and precision engineering, offers a diverse portfolio of pneumatic valves tailored to meet stringent industry demands. From their robust process and high-precision control valves to their compact and efficient directional control valves, Bürkert exemplifies the cutting-edge technology and versatility achievable in modern pneumatic valve design. A fundamental understanding of the principles underlying these technologies, irrespective of the specific manufacturer, empowers professionals to harness the full potential of pneumatics and achieve seamless automation across various applications.
Core Components of a Pneumatic Valves
At the heart of any pneumatic system lies the pneumatic valve, a meticulously engineered device responsible for orchestrating compressed air flow. To truly grasp their operation, we must delve into the core components that constitute these intricate mechanisms.
A. The Valve Body
The valve body serves as the structural backbone, providing a robust housing for the internal components and ensuring their precise alignment. Typically constructed from durable materials like brass, stainless steel, or engineered polymers, the valve body is designed to withstand the rigors of industrial environments, including fluctuations in pressure and temperature. It incorporates precisely machined internal passages and ports that guide the airflow according to the valve’s specific function.
B. Actuators
Actuators are the driving force behind valve operation and are responsible for initiating the movement of internal elements that modulate airflow. They convert an external signal, be it pneumatic, electrical, or mechanical, into the precise motion required to shift the valve’s state.
- Pneumatic Actuators: These actuators harness the power of compressed air itself to effect valve movement. Applying air pressure to a designated chamber within the actuator creates a force imbalance, driving a piston or diaphragm that, in turn, shifts the valve’s internal mechanism. This design is particularly advantageous when electrical signals are impractical or hazardous.
- Solenoid Actuators: Employing the principles of electromagnetism, solenoid actuators provide rapid and precise valve control. An electric current passing through a solenoid coil generates a magnetic field, which attracts or repels a ferromagnetic plunger. This linear motion of the plunger is then translated into the desired valve action, offering exceptional responsiveness and remote control capabilities. Solenoid valves utilize these actuators to efficiently regulate fluid and gas flow in various industrial applications. Their ability to provide swift and accurate operation makes them essential components in automated systems, ensuring reliability and performance in critical processes.
- Mechanical Actuators: These actuators rely on direct physical interaction to operate the valve. They encompass a range of mechanisms, including manual levers, push buttons, rollers, and cams. While offering simplicity and direct control, mechanical actuators are often favored for applications requiring manual intervention or where other actuation methods are unsuitable.
C. Spool or Poppet
Within the valve body reside the critical elements that directly control the passage of compressed air: the spool or poppet. These internal components dictate how air flows through the valve, determining its functionality.
- Spool Valves: Featuring a cylindrical or conical spool that slides within the valve body, spool valves offer exceptional versatility in directing airflow. Different ports are interconnected by moving the spool axially, enabling a wide range of functions, including opening, closing, diverting, and merging air streams. The precision machining of the spool and valve body ensures accurate alignment and minimal leakage.
- Poppet Valves: Employing a disc or ball-shaped poppet that seals against a precisely machined seat, poppet valves excel in providing tight shut-off and rapid actuation. The poppet’s movement, either linear or rotational, controls the opening and closing of the airflow passage. Their robust design and positive sealing action make them well-suited for high-pressure applications and scenarios demanding minimal leakage.
A comprehensive understanding of the interplay between these core components—the valve body, actuator, and spool or poppet—is paramount for engineers and technicians working with pneumatic systems. This foundational knowledge enables informed decision-making during system design, component selection, and troubleshooting, ultimately optimizing performance, efficiency, and safety.
Types of Pneumatic Valves and Their Working Principles
Pneumatic valves exhibit diversity, and each type of valve is meticulously engineered to fulfill specific control objectives within fluid power systems. This section delves into the operational intricacies of these valves, categorizing them based on their primary functions and elucidating their underlying working principles.
A. Directional Control Pneumatic Valves: The Traffic Controllers of Airflow
Directional control valves govern the path of compressed air, selectively directing its flow to different parts of the pneumatic system. These valves act as traffic controllers, enabling precise airflow routing to actuators, cylinders, and other pneumatic components.
- 2-Way Valves: The simplest form, 2-way valves possess two ports and function as on/off switches, either permitting or blocking airflow. They are commonly employed in applications requiring straightforward control, such as filling or venting a pneumatic reservoir.
- 3-Way Valves: Equipped with three ports, 3-way valves offer enhanced control by directing airflow to one of two output ports while blocking the other. They are frequently used to control single-acting cylinders, where air pressure extends the piston, and the spring force retracts it.
- 4-Way Valves: Offering the highest degree of directional control, 4-way valves possess four ports and can direct airflow to two alternative output paths. This enables precise control of double-acting cylinders, facilitating extension and retraction by selectively pressurizing the appropriate cylinder chamber.
- 5-Way Valves: Building upon the 4-way valve, 5-way valves incorporate an additional exhaust port, providing a dedicated path for venting air from the system. This enhances control and efficiency, particularly in applications requiring rapid actuation and precise positioning.
- Specialized Directional Control Valves: Beyond these fundamental types, specialized directional control valves cater to specific applications. Check valves permit unidirectional flow, preventing backflow. Shuttle valves select the higher of two input pressures, while rotary valves offer multi-port control for complex routing scenarios.
B. Flow Control Pneumatic Valves: The Regulators of Airflow Rate
Pneumatic valves are categorized by their functions, each designed for specific control tasks. Let’s explore their operational intricacies:
- Needle Valves: Employing a finely threaded needle to adjust the orifice size, needle valves provide precise and incremental flow control. Their fine-tuning capability makes them suitable for applications demanding accurate speed regulation.
- Throttle Valves: Utilizing a variable restriction, such as a butterfly or ball valve, throttle valves offer a wider range of flow control. They are often employed in applications requiring coarse adjustment or requiring larger flow capacities.
- Pressure Regulators: Pressure regulators ensure stable and predictable actuator performance by maintaining a consistent downstream pressure despite fluctuations in upstream pressure. They are crucial for applications where precise pressure control is paramount, such as in robotic systems or delicate handling processes.
C. Pressure Control Pneumatic Valves: The Guardians of System Pressure
Pressure control valves safeguard pneumatic systems by managing and limiting pressure levels, preventing overpressure conditions that could damage equipment or compromise safety.
- Relief Valves: Acting as safety devices, relief valves open automatically when pressure exceeds a predetermined threshold, venting excess air to protect downstream components. They are essential for preventing catastrophic failures due to overpressure.
- Safety Valves: Similar to relief valves, safety valves provide overpressure protection but are typically designed for higher-pressure applications and offer a larger venting capacity.
- Pressure-Reducing Valves: Maintaining a constant downstream pressure lower than the upstream pressure, pressure-reducing valves ensure optimal operating conditions for specific components or subsystems. They commonly regulate pressure on delicate instruments or actuators requiring lower operating pressures.
Understanding these valve types and their operation enables engineers to select the right valve for each application, optimizing system performance and safety.
Pneumatic Valves: Essential Across Industries
Pneumatic valves are indispensable across diverse sectors, enabling automation and control. Here’s a glimpse into their key applications:
- Manufacturing: Powering robotic arms, controlling clamps, and ensuring precise movements in production lines.
- Process Industries: Regulating fluid flow, pressure, and mixing in chemical and pharmaceutical production.
- Transportation: Critical for braking systems, suspension control, and door operation in heavy vehicles and trains.
- Medical & Food: Enabling precise and hygienic control in ventilation, surgical tools, and food processing.
The versatility and reliability of pneumatic valves make them essential for modern automation across numerous industries.
To sum up, pneumatic valves are complex devices that use compressed air to provide accurate and dependable control in various settings. The valve body, actuator, and flow control elements (spool or poppet) interact to determine how they operate. Engineers and technicians may choose, implement, and maintain pneumatic systems for maximum performance, efficiency, and longevity by knowing the subtleties of these parts and how they work together.
Pneumatic valves are essential to many automated operations, controlling system pressure, regulating flow rate, or guiding airflow. Professionals can troubleshoot issues, enhance system design, and guarantee safe and dependable operation across various sectors by thoroughly understanding their guiding principles. Pneumatic valves continue to play a crucial part in automation. Therefore, proficiency with them is essential for anyone working in fluid power technology.
Published by Carol Jones
My aim is to offer unique, useful, high-quality articles that our readers will love. Whether it is the latest trends, fashion, lifestyle, beauty , technology I offer it all View more posts
Recent Post
How To Wear Red Blush Like A Pro
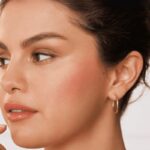